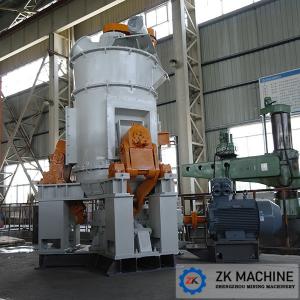
Add to Cart
Novelty Structure Vertical Grinding Mill/Vertical Roller Mill The Technical Process Is Simple
Operation of the Mill and its Description:
After the mill is started in the starting sequence, the material is fed at the set value, the hydraulic system is operated to drop the grinding roller, the oil pump motor of the hydraulic station is turned on, the working pressure of the hydraulic system is adjusted to balance the system, and the separator rotor speed should be adjusted to make The fineness of the product meets the requirements.(The specific method is to first adjust the separator to a higher speed, and adjust the rotor speed according to the product sampling analysis results to obtain the required fineness).
During operation, the temperature of the gas entering and exiting the mill should be adjusted according to the moisture content of the material. The greater the moisture content of the material, the higher the temperature of the gas entering and exiting the mill, but the highest temperature of the milling gas should not exceed 300°C.
Comparison between Ball Mill and Vertical Mill:
Because of the different methods and principles of ball mills and vertical mills, the energy consumption of ball mills is generally higher than that of vertical mills, but this also has certain limitations. When the grinding particle size is greater than 13μm (about 1000 mesh), vertical mills are used. The energy consumption of the mill is lower. When the grinding particle size is less than 13μm, the energy consumption of the ball mill will be lower. The main reason is that when the vertical mill is grinding, the number of times the material passes through the grinding roller and the grinding disc is only one time. The medium-sized powder produced after the rolling is more, and the fine powder is less. The unqualified ones that have been sorted by the classifier Because the fine powder is relatively light, it is difficult to fall on the grinding disc for secondary grinding. Therefore, the ultra-fine powder produced by the vertical mill has lower output and higher energy consumption. The principle of the ball mill is just the opposite. The number of pulverization and grinding is multiple and uncertain, and there is a certain degree of over-grinding. Therefore, the proportion of fine powder ground by the ball mill is also relatively high, and the output when grinding fine powder is relatively high, and the energy consumption is low.
Model | Grinding plate(mm) | output(t/h) | output(×10kt/a) | Main motor power(kW) | |||||
diameter | Pitch | blast furnace slag | cement | Raw meal | blast furnace slag | cement | Raw meal | ||
ZKRM08.2 | 1200 | 800 | 1.5~2 | 3~4 | 6~8 | 1.5 | 3 | 5.5 | 55 |
ZKRM11.2 | 1500 | 1100 | 3~4 | 5~6 | 10~12 | 3 | 4.5 | 9 | 110 |
ZKRM13.2 | 1700 | 1300 | 8~9 | 11~13 | 20~22 | 6 | 9.5 | 17 | 185 |
ZKRM15.2 | 1900 | 1500 | 9~10 | 14~16 | 26~34 | 8 | 12 | 24 | 250 |
ZKRM17.2 | 2100 | 1700 | 12~14 | 20~23 | 40~50 | 10 | 17 | 36 | 355 |
ZKRM19.2 | 2300 | 1900 | 15~17 | 24~26 | 50~60 | 13 | 20 | 43.5 | 450 |
ZKRM20.2 | 2400 | 2000 | 18~20 | 27~30 | 60~75 | 15 | 22.5 | 55 | 560 |
ZKRM22.3 | 2600 | 2200 | 23~25 | 40~50 | 85~110 | 20 | 35.5 | 77 | 710 |
Remarks: the basic standard for vertical mill is as follow:
(1)Power consumption:slag≤25kWh/t,cement≤18kWh/t,raw meal≤9kWh/t;
(2)Moisture content:slag≤15%,cement≤3%,raw meal≤7%;
(3)Ffinished product fineness: specific surface area of slag 4200~4500cm²/g,specific surface area of cement 3300~380 cm²/g,raw meal fineness-80μmR 12~15%;
(4)Moisture content of refined powder:slag 0.5~1.0%,cement 0.5~1.0%,raw meal 0.5~1.0%;
(5)The specific installed capacity and parameters can be adjusted properly according to actual material nature.
(6)The above parameters are applicable for granular blast furnace slag, cement and raw meal and the model selection is determined by material property.